1. Material Characteristics
Chrome Spray Paint
•Composition: Spray paint is a coating based on acrylic or polyurethane resins, mixed with metallic powders (e.g., aluminum) to create a reflective effect resembling chrome plating.
•Thickness: The coating is very thin, usually at the micron level, serving primarily as decoration.
•Adhesion: Relies on primer and surface treatment, prone to peeling or scratching.
Electroplated Chrome
•Composition: Metal chromium is electroplated onto the surface of an object through an electrochemical process, forming a uniform metallic layer.
•Thickness: The thickness of the electroplated layer typically ranges from 0.25 to 20 microns, depending on application requirements.
•Adhesion: Strongly bonded to the substrate, offering superior durability.
2. Process Differences
Chrome Spray Paint
•Application: Directly sprayed onto the wheel surface; quick to complete.
•Equipment Requirements: Does not require complex equipment, suitable for small-scale applications.
•Cost: Lower, considered a budget-friendly solution.
Electroplated Chrome
•Application: Involves multiple steps, including degreasing, polishing, and electroplating.
•Equipment Requirements: Requires specialized electroplating equipment and strict operating conditions.
•Cost: Higher, but delivers professional and long-lasting surface treatment results.
3. Effect Comparison
Appearance
•Chrome Spray Paint: Produces a mirror-like effect but lacks the luster and reflectivity of real chrome plating. While it may appear similar from a distance, details are noticeably inferior.
•Electroplated Chrome: Offers deep, uniform mirror-like reflection, with a high-end visual quality.
Uniformity
•Chrome Spray Paint: May exhibit color inconsistencies or uneven coverage, particularly on complex geometric shapes.
•Electroplated Chrome: Achieves uniform layer distribution, adapting to complex shapes with a flawless surface.
4. Durability
Chrome Spray Paint
•Wear Resistance: Easily scratched and not resistant to heavy abrasion.
•Oxidation Resistance: Tends to fade or bubble when exposed to outdoor or humid environments.
•Corrosion Resistance: Poor weather resistance; prolonged use may result in peeling.
Electroplated Chrome
•Wear Resistance: High hardness (chromium has a Mohs hardness of 8.5), resistant to daily scratches.
•Oxidation Resistance: Strong resistance to air and water corrosion.
•Corrosion Resistance: Suitable for various harsh environments, such as salt spray and muddy water.
5. Application Scenarios
Chrome Spray Paint
Ideal for:
•Short-term decorative needs: Such as exhibition displays or infrequently used items.
•Budget-conscious projects: For example, surface decoration of non-critical components.
•DIY enthusiasts: A cost-effective way to experiment with visual changes.
Electroplated Chrome
Ideal for:
•Long-term durability: Such as car wheels, motorcycle parts, and other high-use components.
•High-end visual appeal: For luxury vehicles or custom modifications.
•Environments with high weather resistance demands: Such as coastal areas or winter regions with heavy salt use.
Summary: Why Spray Paint Cannot Replace Electroplating
1.Durability Gap: Spray paint is vulnerable to environmental effects, whereas electroplated layers provide lasting protection.
2.Visual Quality: Spray paint cannot replicate the deep gloss and reflectivity of chrome plating.
3.Different Use Cases: Spray paint is better for short-term decoration, while electroplating is the long-term solution.
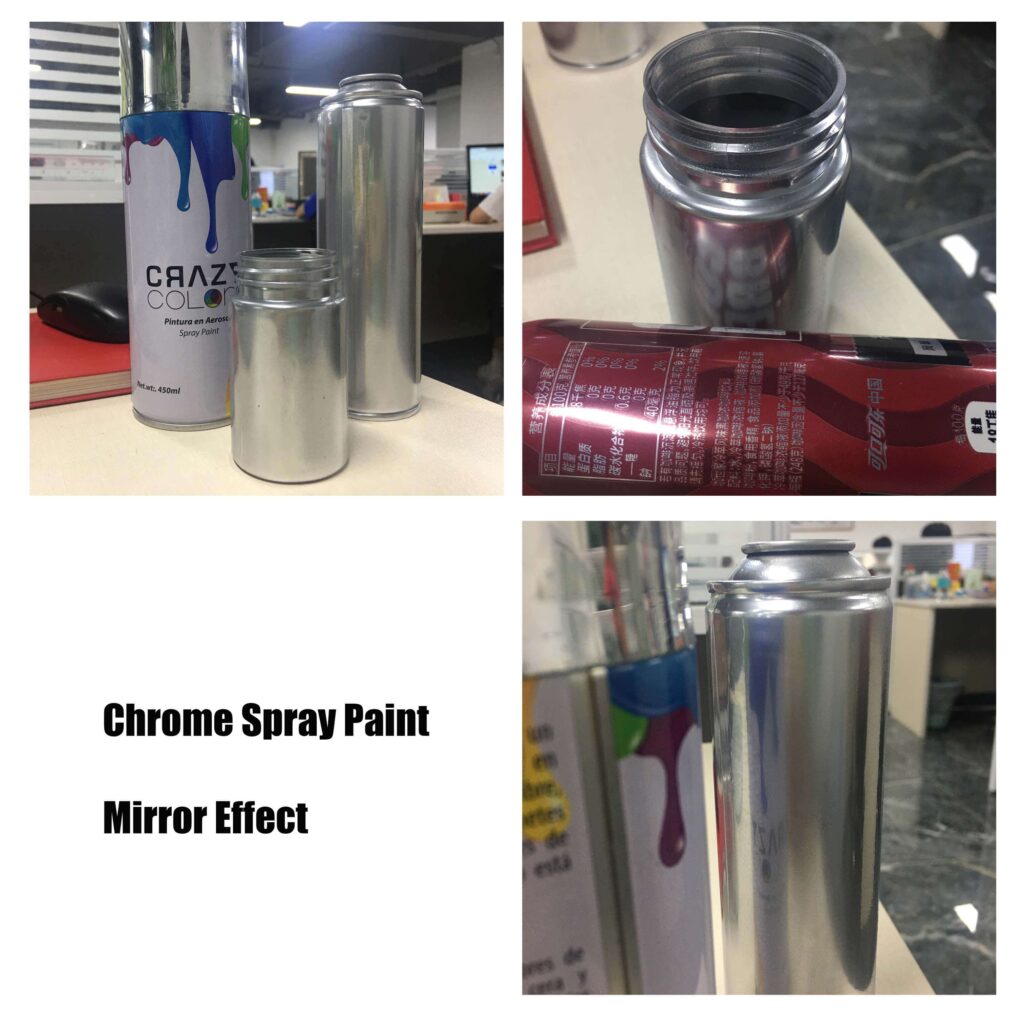